Request a call back
Core Elements of H&S
ISO 45001:2018 compliance at workplace
ISO 45001:2018 specifies requirements for an occupational health and safety (OH&S) management system, and gives guidance for its use, to enable organizations to provide safe and healthy workplaces by preventing work-related injury and ill health, as well as by proactively improving its OH&S performance.
ISO 45001:2018 is applicable to any organization that wishes to establish, implement and maintain an OH&S management system to improve occupational health and safety, eliminate hazards and minimize OH&S risks (including system deficiencies), take advantage of OH&S opportunities, and address OH&S management system nonconformities associated with its activities.
We impart training to create awareness about the ISO 45001:2018 clauses and how the management system can be implemented smoothly to attain and retain the certifications.
Duration: Half day/Full day
Training Mode: Face to Face/ Virtual / Live Demonstration
Scope: Training content, Delivery, Awarding Certificate
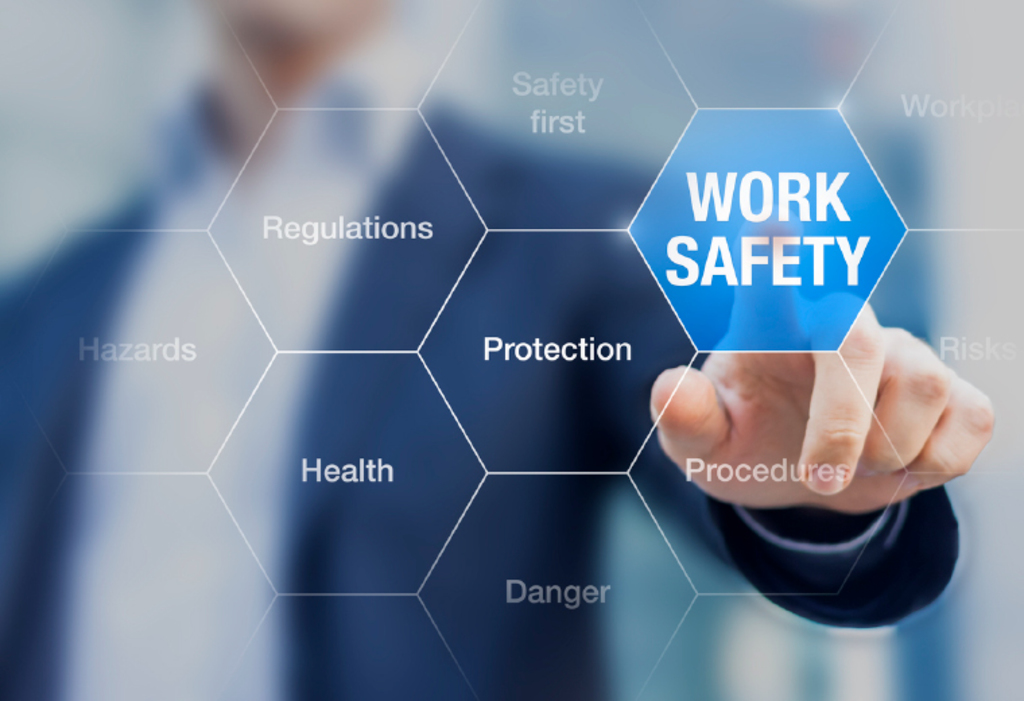
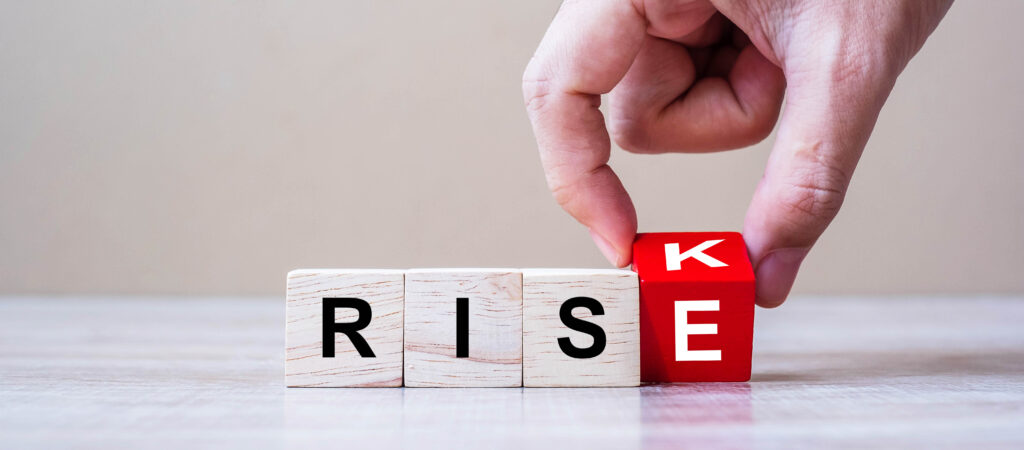
Risk Assessment (HIRA)
Risk assessment is a term used to describe the overall process or method where you:
• Identify hazards and risk factors that have the potential to cause harm (hazard identification).
• Analyze and evaluate the risk associated with that hazard (risk analysis, and risk evaluation).
• Determine appropriate ways to eliminate the hazard, or control the risk when the hazard cannot be eliminated (risk control).
A risk assessment is a thorough look at your workplace to identify those things, situations, processes, etc. that may cause harm, particularly to people. After identification is made, you analyze and evaluate how likely and severe the risk is. When this determination is made, you can next, decide what measures should be in place to effectively eliminate or control the harm from happening.
Why is risk assessment important?
Risk assessments are very important as they form an integral part of an occupational health and safety management plan. They help to:
• Create awareness of hazards and risk.
• Identify who may be at risk (e.g., employees, cleaners, visitors, contractors, the public, etc.).
• Determine whether a control program is required for a particular hazard.
• Determine if existing control measures are adequate or if more should be done.
• Prevent injuries or illnesses, especially when done at the design or planning stage.
• Prioritize hazards and control measures.
• Meet legal requirements where applicable.
Our training on hazard identification & risk assessment (HIRA) specific to the need of the operations helps the employer to mitiate the risk as low as reasonably practically possible.
Duration: Half day/Full day
Training Mode: Face to Face/ Virtual / Live Demonstration
Scope: Training content, Delivery, Awarding Certificate
Job safety analysis & Permit to work system
Before developing a JSA it is essential to understand the value of a JSA. The success of a JSA is dependent on the knowledge of those performing it and their attitude and commitment to it.
It is important to note that a JSA is not a ‘personal prestart check’ or ‘permit to work’. A JSA is also not a compliance activity but it is a key step in workers protecting themselves. Keeping the JSA relevant is a challenge and all involved in the process of conducting a JSA need to have a clear understanding of its purpose.
When the JSA has been done, it can be used to tell the worker how to do the job, and is ideal for training, since it shows a worker how to do the job in the best and safest way. It also sets the standard for the job so that everyone learns to do the job in the same safe way.
The JSA can help managers and supervisors learn about the jobs to be supervised, even if they have not actually done all the jobs themselves. The JSA should be used as a checklist when doing safety inspections or audits, as it tells the auditor what should be happening on any job.
Our trainers help you to align JSA with Permit to work system such that you control human error at workplace and saves your activities from any untoward incident.
Duration: Half day/Full day
Training Mode: Face to Face/ Virtual
Scope: Training content, Delivery, Awarding Certificate
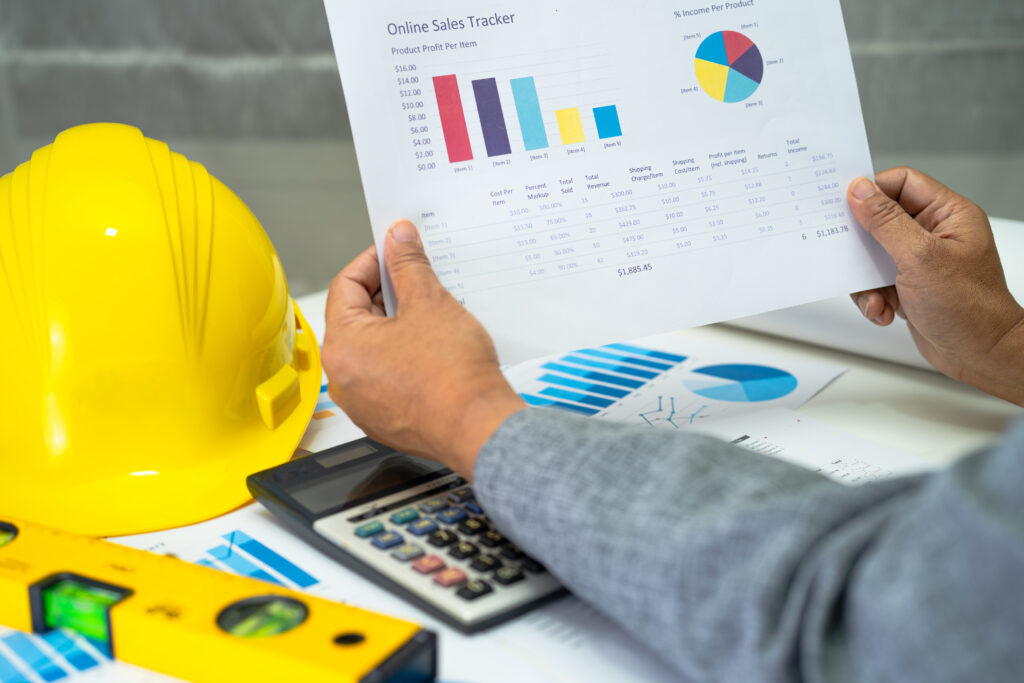
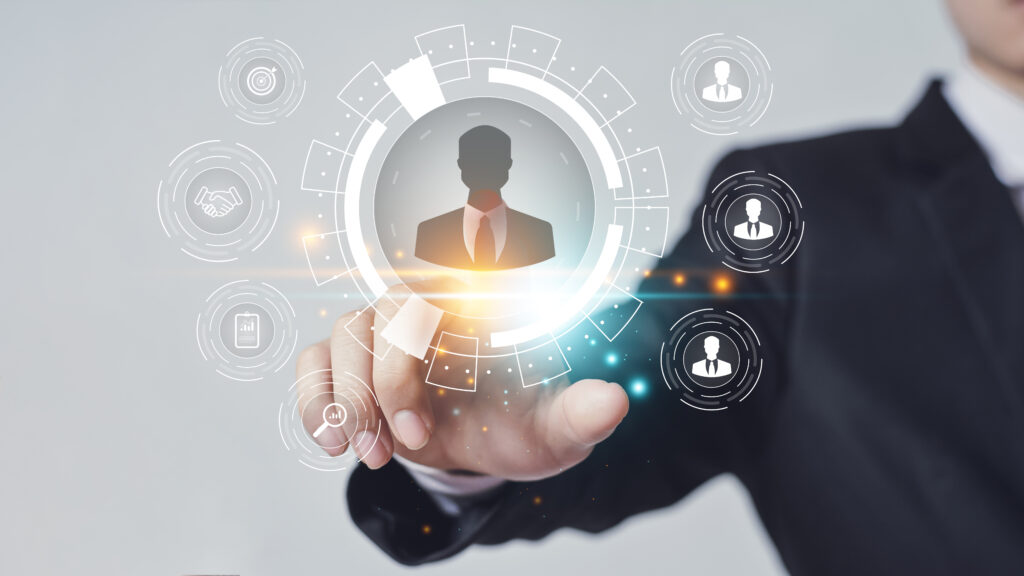
Incident investigation:
The prime reason for an investigation of any industrial accident is to prevent the recurrence of that accident. Simply put, finding out the causes of accidents is very helpful in controlling or eliminating such accidents in the future. To understand the causes of any accident that occurs in an organization / work site, why and how this accident happened, investigators need to gather all the facts pertaining to before and during the incident.
In order to deal with an emergency, it becomes necessary to initiate an accident investigation as well as document steps that are taken. Speed and time frame becomes very important in this whole process to make it successful.
People-centric accident prevention methodologies are increasingly gaining popularity within the HSE field. The finesse of human observation has been proven time and again as the critical factor which enables proactive safety for all.
Duration: Half day/Full day
Training Mode: Face to Face/ Virtual
Scope: Training content, Delivery, Awarding Certificate
Internal audit
Safety audits help you determine how effective your safety programs are, and we believe they are an essential piece of your safety management system. Safety audits can be performed internally by supervisors and employees, or by third-party auditors when you need an independent, non-biased audit of your operations.
Safety audits and inspections have been shown to reduce the number of accidents, so it is something that benefits most employers. We recommend that you be proactive with safety, rather than waiting for an accident to happen. If you lack the resources to do site inspections and audits in-house, you can outsource these services to us.
Our highly competent trainers make it lucid to conduct audit at workplace and make your business ready to face any external audits.
Duration: Half day/Full day
Training Mode: Face to Face/ Virtual
Scope: Training content, Delivery, Awarding Certificate
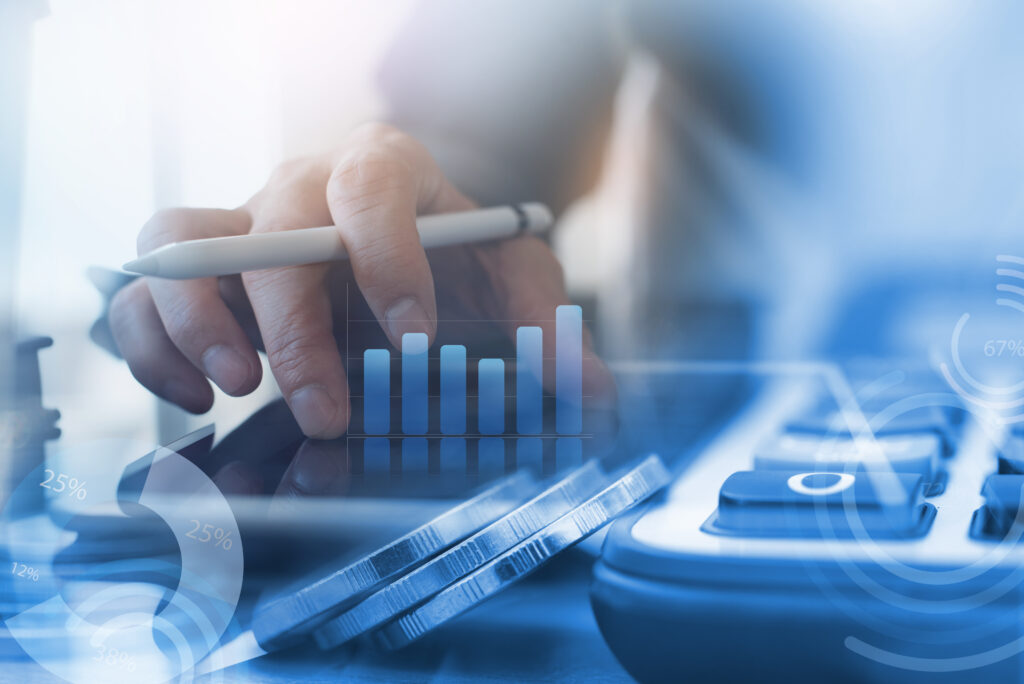